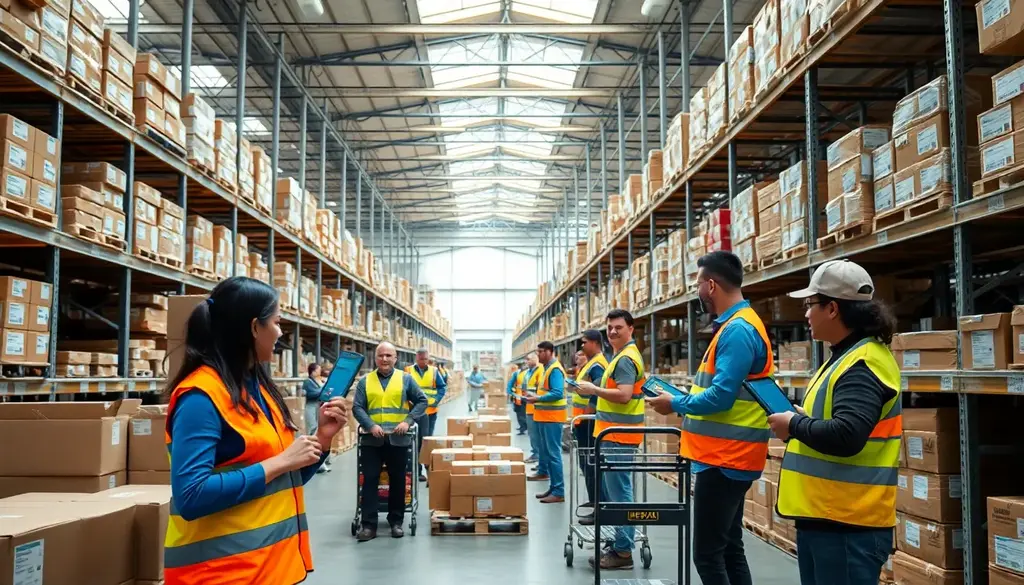
In the fast-paced world of warehouse management, the efficiency of order fulfillment and inventory control is paramount. Picking labels play a crucial role in streamlining these processes, serving as a critical tool in modern logistics operations. This guide explores the significance of picking labels in warehouse management, detailing how they enhance operational workflows and support the coordination of complex logistics tasks. By understanding the function and impact of picking labels, professionals in the supply chain and logistics sectors can optimize their operations for better accuracy, speed, and overall efficiency.
Understanding Picking Labels in Warehouse Management
Picking labels are essential tools in warehouse operations, designed to aid in the accurate identification and retrieval of items during the order fulfillment process. These labels provide critical information that helps staff quickly locate goods, thereby reducing errors and increasing productivity.
Definition and Importance
Picking labels are adhesive tags that can be attached to shelves or individual items. They typically feature barcodes or QR codes that workers can scan to confirm the item’s identity, location, and other pertinent data. The use of picking labels minimizes the likelihood of human error, ensuring that the correct items are always picked and processed.
Integration with Warehouse Management Systems
Picking labels are integral to modern Warehouse Management Systems (WMS). They work by providing real-time data that helps maintain accurate inventory records. When items are scanned, the WMS updates instantly, reflecting current stock levels and helping managers make informed decisions about reordering and stock allocation.
Types of Picking Labels and Their Uses
Different warehouse environments and tasks require specific types of picking labels. Understanding the various options available and their applications can significantly enhance operational efficiency.
Detailed Exploration of Various Types
There are several types of picking labels, including:
- Single-line labels: These contain basic information, such as product codes or location data.
- Multi-line labels: These offer more detailed information, which can include the order number, item description, and special handling instructions.
- Radio frequency identification (RFID) tags: These are used for automated tracking and data collection, enhancing the speed and accuracy of inventory management.
Specific Applications in Different Warehouse Scenarios
Each type of label serves a unique purpose:
- Single-line labels are often used in smaller operations where simplicity and speed are key.
- Multi-line labels are suitable for complex operations that handle a variety of products and require detailed information for accurate processing.
- RFID tags are ideal for high-volume environments where automation can lead to significant efficiency gains.
The Impact of Picking Labels on Inventory Management
Picking labels are more than just tools for identifying products; they are integral to maintaining accurate and reliable inventory management systems.
Contribution to Accurate Inventory Tracking and Control
By ensuring that every item is correctly labeled and accounted for, picking labels help maintain precise inventory records. This accuracy is crucial for effective stock management, preventing overstocking and stockouts, and facilitating a smoother supply chain operation.
Case Studies Showing Improvements in Inventory Accuracy
Several case studies highlight the effectiveness of picking labels in improving inventory accuracy. For instance, a retail warehouse reported a 25% decrease in picking errors after switching to multi-line barcode labels, directly impacting their bottom line by reducing returns and lost sales.
Streamlining Order Fulfillment with Effective Labeling Strategies
Optimizing the use of picking labels can significantly enhance the order fulfillment process, making it faster and more reliable.
Techniques for Optimizing the Use of Picking Labels
Effective strategies include:
- Customizing label information to fit the specific needs of the warehouse operations.
- Regular updates and maintenance to ensure labels are always accurate and readable.
- Training staff on the best practices for scanning and handling labeled items.
Benefits of Tailored Picking Label Strategies
Customized picking label strategies can lead to:
- Reduced time spent on locating and verifying items.
- Fewer errors in shipping and receiving.
- Improved overall customer satisfaction due to faster and more accurate deliveries.
Integrating Picking Labels with Logistics Coordination
The synchronization of logistics operations is crucial for the seamless movement of goods from suppliers to customers. Picking labels play a vital role in this coordination.
Role of Picking Labels in Synchronizing Logistics Operations
Picking labels provide the necessary data that logistics partners need to ensure that the right products are at the right place at the right time. This integration is crucial for just-in-time delivery systems and for maintaining lean inventory levels.
Examples of Successful Logistics Coordination
Successful implementations include the use of RFID tags in a multinational manufacturing firm, which helped reduce shipment errors by 30% and improved the efficiency of their supply chain.
Choosing the Right Picking Labels: Providers and Considerations
Selecting the right picking labels involves understanding the specific needs of your warehouse and evaluating the offerings of various providers.
Review of Top Providers
Some of the leading providers in the market offer advanced solutions that integrate seamlessly with existing WMS and provide high-quality, durable labels suitable for various environments.
Key Factors to Consider
When choosing a provider, consider:
- Compatibility with existing systems.
- Range of label options.
- Provider’s reliability and support services.
Picking labels are indispensable tools in modern warehouse management, crucial for enhancing inventory accuracy and streamlining order fulfillment. By understanding the different types of labels available and integrating them effectively into your operations, you can achieve greater efficiency and coordination. Choosing the right labels and providers is essential for leveraging these benefits to their fullest potential.
FAQ Section
Q1: What are the primary benefits of using picking labels in warehouse management?
A1: Picking labels enhance operational efficiency, reduce errors in order fulfillment, and improve inventory tracking and management.
Q2: How do picking labels integrate with warehouse management systems?
A2: Picking labels work in tandem with warehouse management systems to provide real-time data updates, facilitate better inventory control, and streamline order processing.
Q3: Can the use of picking labels reduce operational costs?
A3: Yes, by minimizing errors and improving the speed of order processing, picking labels can significantly reduce labor costs and waste in warehouse operations.
Q4: What should I consider when choosing a provider for picking labels?
A4: Consider factors such as the provider’s technology compatibility with your existing systems, the variety of label options offered, and their reputation for reliability and service.
Q5: Are there environmentally friendly options for picking labels?
A5: Many providers now offer sustainable options for picking labels, including recyclable materials and eco-friendly adhesives, catering to environmentally conscious businesses.