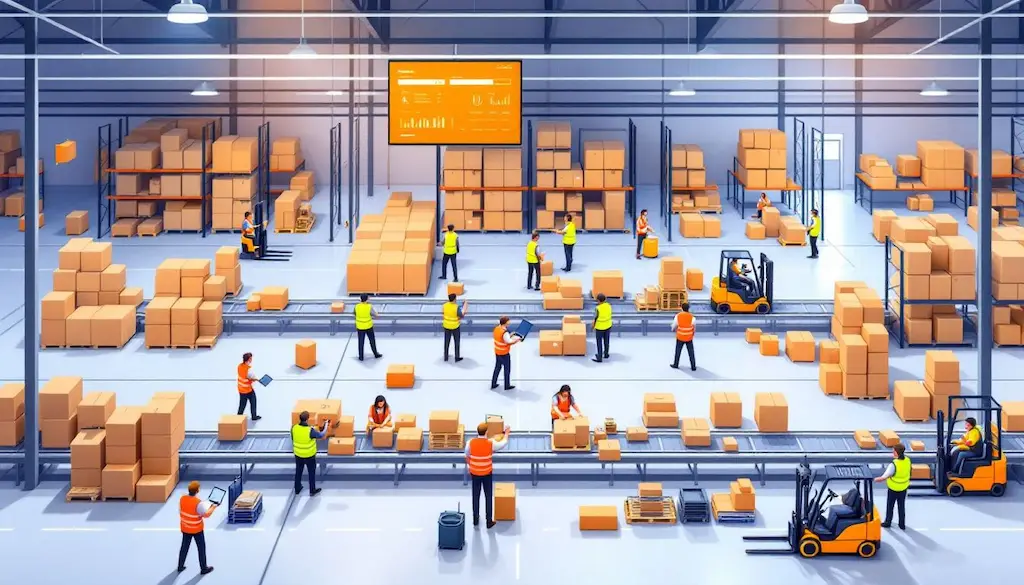
Pick pack ship optimizes warehouse operations by ensuring accurate picking, secure packing, and efficient shipping of items. In this guide, you’ll learn detailed strategies to enhance each step, reducing errors and speeding up fulfillment to boost customer satisfaction.
Key Takeaways
- The pick pack ship process consists of three crucial stages: picking, packing, and shipping, each requiring best practices for efficiency and accuracy.
- Selecting the appropriate picking strategy—piece, batch, zone, or wave—is essential to optimizing warehouse operations based on business needs and order volume.
- Implementing specialized software and automation can enhance warehouse efficiency, reduce labor costs, and improve inventory management, while outsourcing can provide scalability and advanced technology access.
Understanding Pick Pack Ship
The pick pack ship process is fundamental to efficient warehouse operations. It encompasses three stages: the picking process, packing items securely, and shipping them to customers. The journey starts with picking, where items are selected from the warehouse according to a pick list. Seamless integration with omnichannel sales systems ensures accuracy and efficiency during this stage.
After picking, items move to packing stations where they are organized and prepared for shipping. Secure packing prevents damage during transit. The final stage, shipping, involves selecting the appropriate carrier, creating accurate labels, and offering real-time tracking to customers. Each step is vital for maintaining an organized workflow and improving order fulfillment accuracy.
Mastering the nuances of each stage and implementing best practices can greatly enhance your warehouse’s efficiency. The following sections provide practical insights and strategies for each component of the pick pack ship process.
The Picking Process
The picking process initiates order fulfillment and sets the tone for subsequent operations. Various strategies can be employed based on the business nature and order volume, including piece picking, batch picking, zone picking, and wave picking. Each method has distinct advantages suited to different warehouse operations.
Selecting the optimal picking strategy is key to efficiency and timely order fulfillment. Order volume, warehouse size, and product range are significant factors in determining the best method.
The following subsections explore these strategies in detail to help you make informed decisions for your warehouse operations.
Piece Picking
Piece picking, the most basic method, involves selecting items for one order at a time. This approach suits small ecommerce businesses with fewer daily orders. Although straightforward, piece picking can be inefficient for larger operations due to increased travel time for warehouse workers.
For smaller operations, it ensures accuracy and minimizes the risk of missing or incorrect items.
Batch Picking
Batch picking involves selecting items for multiple orders simultaneously, thereby significantly improving efficiency by reducing travel time and maximizing productivity. This method is widely used in ecommerce and distribution centers where quick order fulfillment is essential.
Effective batch picking relies on advanced fulfillment software, like a Warehouse Management System (WMS) or an Order Management System (OMS), to streamline operations and ensure accuracy.
Zone Picking
Zone picking organizes the warehouse into designated areas, each managed by specific pickers. This method works best for larger warehouses with high order volumes and a diverse range of SKUs. By reducing travel time for pickers and increasing overall efficiency, zone picking ensures prompt and accurate order fulfillment.
Wave Picking
Wave picking combines elements of batch and zone picking. Items are selected for multiple orders within assigned zones at specified times, optimizing the process for high-performing businesses with thousands of monthly orders. This method benefits distribution centers and ecommerce warehouses with high order volumes and a diverse range of SKUs.
Wave picking offers streamlined operations, improved efficiency, faster processing times, and increased accuracy. Incorporating scheduling windows ensures picking operations meet shipping deadlines, further enhancing fulfillment efficiency.
The Packing Process
After picking, the next stage is packing. This involves placing items in appropriately sized boxes using suitable materials to ensure they reach customers in perfect condition. The packing process is crucial for efficient warehouse operations, impacting shipping costs and customer satisfaction. Using materials like bubble wrap and packing peanuts keeps items safe during transit.
Accurate packing techniques involve verifying items against the order and minimizing the use of oversized boxes to reduce shipping costs. Specialized software can help determine the right box sizes and packing materials, enhancing the process and ensuring proper documentation, like packing slips.
The following subsections delve into key components of the packing process, offering practical tips for optimization.
Right-Sized Boxes
Appropriately sized boxes minimize additional shipping expenses and reduce product damage. Compact packaging lowers the pick and pack fee based on materials and dimensional weight. Correctly sized boxes limit product movement, significantly lowering the risk of damage during transit.
Selecting the right box sizes is vital for cost efficiency and ensuring products arrive in perfect condition.
Protective Infill
Protective infill materials, also called void fill, like bubble wrap and packing peanuts, prevent items from shifting during transit. By filling empty spaces, protective infill minimizes the risk of damage, ensuring items arrive intact and in good condition.
Proper use of protective infill enhances customer satisfaction by ensuring products arrive without damage.
Secure Sealing
Secure sealing is crucial in the packing process. The choice of packing tape significantly affects the package’s durability and security during transport. Proper sealing prevents packages from opening during transit, reducing the risk of damage and enhancing quality control.
The Shipping Process
The shipping process is the final stage in pick pack ship operations and plays a crucial role in customer satisfaction. It involves selecting the right carrier, creating accurate shipping labels, and providing real-time tracking. Key time considerations include the interval from label creation to shipping and from shipping to delivery.
Shipping labels are essential, including necessary details like the recipient’s address and tracking information. Accurate labels ensure packages reach their destination without issues, minimizing delivery errors and enhancing customer satisfaction.
The following subsections explore key components of the shipping process, offering insights into carrier selection, label creation, and real-time tracking.
Carrier Selection
Choosing the right carrier is essential for optimizing the shipping process. Shipping costs often determine carrier selection, directly impacting overall profitability. Speed and reliability are also critical, especially for ecommerce businesses relying on timely deliveries to satisfy customer expectations.
Evaluating carriers based on cost, speed, and reliability enhances customer service and optimizes shipping operations.
Label Creation
Accurate shipping labels are vital for ensuring packages reach their destination without issues. Best practices include ensuring clarity, accuracy of information, and proper placement on the package.
Using the right packing materials is vital for maintaining package integrity and reducing delivery errors due to the label becoming damaged.
Real-Time Tracking
Real-time tracking allows customers to monitor their packages, enhancing transparency in the shipping process. Tracking numbers help customers set accurate expectations for delivery and inform them of potential delays, significantly enhancing satisfaction.
Benefits of Pick Pack Ship Systems
Implementing a pick pack ship system offers numerous benefits that can transform warehouse operations. Here are some key advantages:
- Cost reduction and the ability to scale efficiently.
- Enhanced operational efficiency.
- Expedited fulfillment.
- Reduced labor costs.
- Minimized errors.
- Ensured customer satisfaction.
These benefits can significantly improve the overall performance of your warehouse operations.
Using specialized software for pick pack ship operations increases accuracy, efficiency, and speed. It also improves inventory management by reducing errors and automating tasks. Integrated data systems support effective supply chain management and prevent data silos, enhancing operational efficiency.
The following subsections delve into the specific benefits of pick pack ship systems.
Speedy Fulfillment
Quick fulfillment is essential as many shoppers consider delivery a key part of their shopping experience. Streamlined processes lead to faster order delivery from the fulfillment center, significantly enhancing customer satisfaction.
Using the right-sized box optimizes carrier costs and helps prevent returns or losses, further speeding up fulfillment.
Reduced Labor Costs
An optimized pick, pack, and ship process significantly lowers labor costs by streamlining workflows and reducing time spent on each order. Effective systems also limit excess inventory, reducing labor costs associated with handling, storing, and managing surplus items.
Inventory Control
Advanced inventory management systems are essential for preventing stock discrepancies and ensuring product availability. By maintaining accurate inventory levels, these systems minimize errors and ensure products are available when needed.
Effective inventory control also reduces the risks of overstocking, optimizing warehouse space and resources.
Overcoming Common Challenges
Common challenges in the pick pack ship process can significantly impact efficiency and profitability. Here are some of the key issues:
- Poorly planned fulfillment operations lead to costly mistakes.
- Long lead times can frustrate customers.
- Reduced customer satisfaction due to inefficiencies.
To address these challenges, optimizing warehouse layouts and utilizing technology, like barcode scanners, can minimize picking errors and boost productivity.
Addressing these challenges is crucial for improving overall operational efficiency and customer satisfaction. The following subsections explore strategies for overcoming these challenges, focusing on planning and layout, avoiding disorganization, and implementing efficient picking strategies.
Planning and Layout
Poor planning and insufficient consideration of warehouse layout lead to inefficiencies in the pick pack ship process. An optimized warehouse layout can significantly shorten picking time, with potential reductions of up to 20%.
When deciding on in-house order fulfillment, consider aspects like quality control, inventory storage, and warehouse management.
Avoiding Disorganization
Cluttered aisles and misplaced items significantly contribute to poor warehouse organization, leading to increased errors. Maintaining an organized warehouse is essential to prevent errors and ensure safety.
An organized warehouse enhances operational efficiency, reduces safety risks, and lowers error rates.
Efficient Picking Strategies
Implementing mobile technology like barcode scanners can boost worker productivity by up to 39% during the pick and pack process. Choosing the right strategy is crucial for optimizing warehouse operations and ensuring timely order fulfillment.
Efficient picking strategies lead to faster order processing, reduced labor costs, and improved customer satisfaction.
Choosing the Right Software
Selecting the right software for pick pack ship operations is critical for streamlining processes and enhancing efficiency. Inventory software organizes inventory and directs the pick pack ship process, improving accuracy and efficiency. Unique features of pick and pack software can vary, with some being purpose-built for specific processes.
Effective warehouse management software can significantly enhance the pick and pack process’s efficiency, automating tasks such as picking assignments, order status, and communication.
The following subsections will discuss the essential features to look for in pick and pack software and the importance of integration capabilities.
Features to Look For
Choosing the right features in inventory management software is crucial for enhancing efficiency in pick pack ship systems. Real-time analytics allow businesses to monitor performance and make timely adjustments, quickly identifying bottlenecks in the fulfillment process and addressing them efficiently.
By focusing on essential features like real-time analytics, businesses can significantly improve their operational effectiveness and customer satisfaction.
Integration Capabilities
Integrated software systems enhance data accuracy and streamline operations across different warehouse functions. By connecting various systems, warehouses can reduce errors, improve the flow of information, and significantly enhance overall efficiency in warehouse operations.
Integration capabilities ensure that all aspects of the pick pack ship process work together seamlessly, from inventory management to real-time tracking.
When to Outsource Pick Pack Ship Operations
Deciding when to outsource pick pack ship operations can be crucial for business growth and efficiency. Companies should consider outsourcing when they face uneven demand, rapid growth, or cost challenges. Outsourcing may be necessary when the in-house order fulfillment process limits business growth, providing scalability and expertise to better manage fulfillment challenges.
Outsourcing pick pack ship operations offers significant benefits, including improved customer service through specialized support from third-party logistics providers (3PLs), access to advanced technology without significant investment, and the flexibility to adapt to market demands while focusing on core business activities.
The following subsections will guide you through evaluating business needs and highlight the benefits of outsourcing.
Evaluating Business Needs
Assessing business needs is crucial in determining whether to outsource logistics operations. Businesses should evaluate their order volumes and logistics capabilities to determine the need for outsourcing. Engaging various managers in the evaluation process ensures a comprehensive understanding of business needs, leading to more informed decisions regarding outsourcing and its impact on operations and costs.
Benefits of Outsourcing
Outsourcing fulfillment allows businesses to quickly scale operations in response to demand fluctuations, leading to improved customer service through the specialized support of a 3PL. Using a 3PL provides access to advanced technology without the need for significant investment, offering businesses the flexibility to adapt to market demands while focusing on core business activities.
Argos Software: Your Trusted Partner for Pick Pack Ship Excellence
In the fast-paced world of warehouse operations, optimizing the pick pack ship process is essential for maintaining efficiency, accuracy, and customer satisfaction. Argos Software offers an all-in-one solution tailored to meet the unique needs of businesses striving to streamline their operations.
With Argos Warehouse Management Software (WMS), you can take full control of your pick pack ship workflow. Our platform simplifies the complexities of inventory management, order fulfillment, and shipping logistics by integrating advanced features like real-time analytics, automated picking assignments, and seamless carrier integrations.
Here’s how Argos Software helps you succeed:
- Efficiency Boost: Automate repetitive tasks, reduce picking errors, and accelerate order processing with smart workflows and barcode scanning capabilities.
- Inventory Accuracy: Real-time visibility into inventory ensures accurate stock levels, preventing costly overstocking or stockouts.
- Cost Savings: Optimize packing materials and carrier selection to reduce shipping expenses, while minimizing labor costs through improved task coordination.
- Scalability: Whether you’re managing seasonal demand or expanding your operations, our solutions scale effortlessly to meet your growth needs.
- Customer Satisfaction: Real-time tracking and error-free fulfillment enhance transparency and build trust with your customers.
By leveraging Argos Software, you gain a competitive edge, transforming your warehouse into a streamlined, cost-effective powerhouse. Whether you’re a small ecommerce business or a large distribution center, our WMS adapts to your needs, helping you master the pick pack ship process and deliver exceptional results.
Ready to optimize your warehouse operations? Discover more about Argos Software’s WMS solutions and see how we can help you achieve your operational goals.
Summary
The pick pack ship process is a cornerstone of efficient warehouse operations, ensuring that items are accurately picked, securely packed, and promptly shipped to customers. By implementing effective strategies and leveraging advanced tools, businesses can enhance operational efficiency, reduce costs, and improve customer satisfaction.
Argos Software’s Warehouse Management System (WMS) offers a tailored solution to streamline the complexities of the pick pack ship process. With features like real-time analytics, automated workflows, and seamless carrier integrations, Argos Software empowers businesses to optimize operations and scale effortlessly.
Ready to transform your warehouse? Take the first step by exploring how Argos Software’s WMS can help you achieve your goals. Request a Demo Today!
Frequently Asked Questions
What is the pick pack ship process?
The pick pack ship process is crucial for efficient order fulfillment, comprising the steps of selecting items from inventory, securely packing them, and shipping them to customers. This systematic approach enhances accuracy and customer satisfaction.
What are the main picking strategies used in warehouses?
The main picking strategies used in warehouses include piece picking, batch picking, zone picking, and wave picking, each tailored to optimize efficiency based on the warehouse’s size and order volume. Choosing the right strategy can significantly enhance operational productivity.
Why is using the right-sized boxes important in the packing process?
Using the right-sized boxes is crucial as it minimizes shipping expenses, reduces the risk of product damage, and limits movement during transit, ensuring that items arrive safely and on time.
How does real-time tracking benefit the shipping process?
Real-time tracking enhances the shipping process by providing transparency and improving customer satisfaction, as it allows customers to monitor their packages and stay informed about delivery times and potential delays.
When should a business consider outsourcing pick pack ship operations?
A business should consider outsourcing pick pack ship operations when it experiences uneven demand, rapid growth, or cost challenges, as this allows for scalability and access to specialized support and technology from third-party logistics providers.