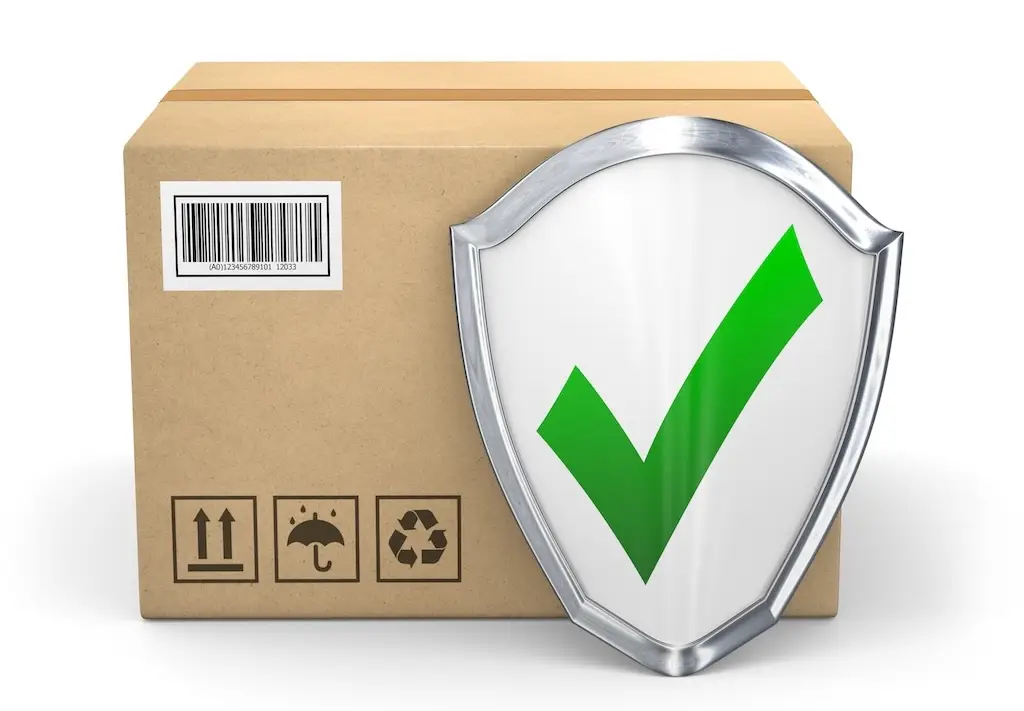
Order picking accuracy is the measure of how accurately items are picked and fulfilled in warehouse operations. High accuracy is crucial because it directly impacts customer satisfaction and operational efficiency. In this article, we will explore what order picking accuracy entails, why it matters, and effective strategies to improve it.
Key Takeaways
- Order picking accuracy is crucial for customer satisfaction and operational success; high accuracy fosters trust and loyalty.
- Key metrics, such as order picking accuracy rates, should be regularly measured and improved using technology and optimized processes.
- Investing in workforce training and choosing the right fulfillment partner are essential for enhancing order picking accuracy and overall efficiency.
Understanding Order Picking Accuracy
Order picking accuracy is the backbone of efficient warehouse operations. It refers to the percentage of orders that are picked and fulfilled without errors. High order picking accuracy is crucial because it directly impacts customer satisfaction. Prompt and accurate deliveries build customer trust, encouraging repeat purchases and positive word-of-mouth.
On the other hand, inaccurate order picking can have severe repercussions. Mistakes in picking can lead to negative customer experiences, increased return rates, and financial losses. In today’s competitive market, businesses that maintain high accurate order picking accuracy often enjoy a significant competitive advantage, fostering customer loyalty and driving profitability.
Customers expect prompt and accurate order fulfillment. Missing these expectations can damage your reputation and push customers to competitors. Thus, maintaining a high order accuracy rate is crucial for upholding your reputation and operational success.
Key Metrics for Measuring Order Picking Accuracy
Accurate order delivery is a cornerstone of success in eCommerce and fulfillment in general. Key performance indicators (KPIs) like order picking accuracy must be established and regularly measured to ensure operational efficiency and customer satisfaction. While order picking accuracy focuses on the picking stage, order accuracy covers all stages of fulfillment, making it a broader measure.
To improve overall performance, it’s essential to monitor these metrics closely. Setting a goal to boost order accuracy from 90% to 95% by year’s end, for example, can greatly enhance operations. Warehouse management systems (WMS) and order management systems play a key role in minimizing picking errors and ensuring accurate fulfillment.
How to Calculate Order Picking Accuracy Rate
Calculating the order picking accuracy rate is straightforward yet vital for assessing performance. The formula is simple: (Accurate orders fulfilled / Total orders fulfilled) * 100. For instance, if you fulfill 100 orders and make two mistakes, your accuracy rate is 98%. This calculation helps you pinpoint areas that need improvement and track progress over time.
Accurate inventory data is vital for reducing errors and boosting order picking accuracy. To maintain accurate inventory data, real-time inventory updates and automated systems ensure that the correct items are always available, greatly improving accuracy.
Frequent measurement and analysis of your accuracy rate enable informed decisions for better operational efficiency.
Interpreting Your Order Picking Accuracy Rate
Interpreting your order picking accuracy rate is as crucial as calculating it. An order picking accuracy rate between 96-98% is vital for competitiveness in e-commerce. If your accuracy rate falls below 95%, it’s a clear indicator that immediate improvements are necessary to avoid losing customers to competitors.
While achieving 100% accuracy is challenging, striving for it ensures continuous improvement. Regularly reviewing your accuracy rate and setting incremental goals can lead to significant enhancements in your picking process and overall customer satisfaction.
Common Causes of Picking Errors
Picking errors can stem from various sources, but human error is one of the most frequent culprits. Mistakes such as picking the wrong items or quantities can disrupt the entire fulfillment process. Additionally, misplaced items and disorganized inventory can cause significant delays, leading to incorrect orders and dissatisfied customers.
Tips: Lack of prioritization and ineffective warehouse slotting are other common causes of picking errors. Spotting error-prone processes and deploying strategies to reduce human error can greatly improve picking accuracy. Conducting regular audits and leveraging technology to track and organize inventory can alleviate these issues.
Effective Strategies to Improve Order Picking Accuracy
Improving order picking accuracy is a multifaceted endeavor that can lead to increased customer satisfaction and operational efficiency. Begin by assessing your current accuracy rate and setting specific improvement goals. Communicating effectively with the team is key when setting these goals.
Enhancing accuracy involves optimizing picking routes and processes, implementing technology solutions, and improving quality control standards. Keep in mind that small incremental changes can lead to substantial benefits in the long run.
Implementing Technology Solutions
Integrating technology into the picking process can greatly boost accuracy. A warehouse management system automates processes, offering visibility and validation to reduce human error. Meanwhile, barcode labels and scanners effectively check accuracy and update inventory levels in real-time, aiding accurate order fulfillment.
Tip: Integrating WMS and automation technologies streamlines the picking process, resulting in higher order picking accuracy.
Optimizing Warehouse Layout and Processes
An optimized warehouse layout is crucial for enhancing picking accuracy. Fixed item locations can limit flexibility, but effective warehouse slotting organizes inventory in the warehouse space to reduce confusion and enhance precision. Batch picking or zone picking strategies work well for large order volumes. Clear picking routes minimize errors and speed up the picking process.
Enhancing Quality Control Standards
Maintaining high picking accuracy relies heavily on quality control standards. Regular audits and process reviews ensure adherence to quality standards in the picking and packing process. While, accurate inventory data is essential for ensuring the correct items are picked for orders.
Designated locations for partially picked orders as a quality control measure can prevent wasted effort and increased shipping costs.
Training and Engaging Your Workforce
A well-trained and engaged workforce is crucial for enhancing order picking accuracy. Training programs and a culture of accountability can greatly enhance operational efficiency. Regular performance evaluations, employee feedback, and clear objectives help keep staff motivated and focused.
Offering professional growth opportunities and recognizing employee contributions are vital for maintaining motivation and engagement. Investing in training and fostering a supportive work environment can improve order picking accuracy and overall operational success.
Choosing the Right Fulfillment Partner
If your business doesn’t handle its own fulfillment, choosing the right fulfillment partner can streamline order fulfillment processes and support your business’ growth. A reliable fulfillment service should provide performance guarantees and take responsibility for any fulfillment errors. Note that your business size should influence your choice, as smaller providers may better serve small businesses.
Pricing and operational transparency are crucial for building trust with your fulfillment partner. Evaluating potential partners using these criteria ensures seamless and accurate order fulfillment, ultimately enhancing customer satisfaction.
Argos Software: Enabling Accuracy and Efficiency in Warehouse Operations
Argos Software specializes in providing advanced solutions to optimize warehouse operations and elevate order picking accuracy. Our powerful tools and technology help businesses achieve operational excellence, improve customer satisfaction, and stay ahead in a competitive market.
Highlights of Argos Software’s WMS Solution:
- Real-Time Inventory Tracking: Minimize picking errors with up-to-date inventory visibility.
- Process Automation: Streamline workflows to reduce manual effort and enhance accuracy.
- Actionable Analytics: Identify performance gaps and track improvements with comprehensive reporting tools.
- Scalable Solutions: Tailored features that grow with your business, from small operations to enterprise-level needs.
- Seamless Integration: Easily incorporate our WMS with your existing systems for smooth transitions and maximum efficiency.
Summary
In summary, achieving high order picking accuracy is essential for operational success and customer satisfaction. By understanding the importance of accuracy, measuring key metrics, identifying common errors, and implementing effective strategies, businesses can significantly enhance their warehouse operations.
The journey to improved accuracy involves continuous improvement, training, and the right technology and fulfillment partners. Embracing these changes can lead to substantial benefits, ensuring that every customer order is picked with precision and efficiency.
Take your warehouse operations to the next level. Contact Argos Software today to explore our advanced WMS solutions and discover how we can help you achieve unparalleled order picking accuracy.
Frequently Asked Questions
What is order picking accuracy?
Order picking accuracy is the percentage of orders correctly picked and fulfilled without mistakes, which is crucial for customer satisfaction. It means getting the right items to the right people every time.
How do you calculate the order picking accuracy rate?
To calculate the order picking accuracy rate, use the formula: (Accurate orders fulfilled / Total orders fulfilled) * 100. This gives you a clear percentage of how accurate your order picking process is.
What are common causes of picking errors?
Picking errors often stem from human mistakes, disorganized inventory, and misplaced items. To reduce these errors, prioritize organization and thorough training.
How can technology improve order picking accuracy?
Using technology like warehouse management systems and barcode scanners can significantly boost order picking accuracy. These tools automate processes and minimize manual errors, ensuring you have real-time inventory updates.
Why is choosing the right fulfillment partner important?
Choosing the right fulfillment partner is crucial because they can streamline your order processes and boost customer satisfaction through accurate fulfillment. This means happier customers and a more efficient operation for your business.