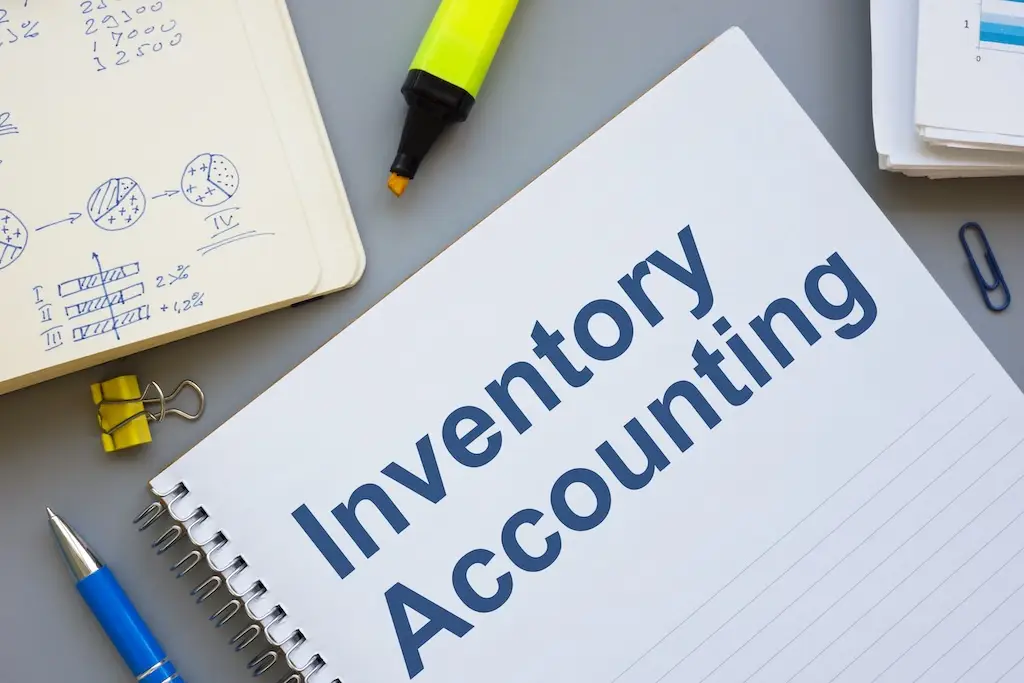
Inventory accounting involves tracking and managing the costs of goods a business holds for sale. It’s essential for determining profitability, meeting tax obligations, and maintaining accurate financial records. This article covers the key methods, components, and best practices of inventory accounting.
Key Takeaways
- Accurate inventory accounting is essential for a company’s financial health, affecting profitability, taxation, and decision-making.
- Choosing the appropriate inventory valuation method (FIFO, LIFO, weighted average, specific identification) significantly impacts financial statements and tax liabilities.
- Implementing effective inventory management techniques and technologies can optimize operational efficiency and enhance accuracy in tracking inventory levels.
Understanding Inventory Accounting
Inventory accounting is more than just keeping track of products—it’s a critical component that impacts a company’s profitability, taxation, and overall financial health. Proper inventory management ensures that businesses can meet their tax obligations and maintain financial visibility, essential for making informed business decisions. Accurate inventory accounting dictates the value of inventory assets, influencing profit and tax calculations. Imagine the implications of discrepancies in inventory levels—these can significantly affect business valuation and operational efficiency.
Key metrics like the inventory turnover ratio are invaluable in guiding business decisions and improving operational efficiency. Understanding the financial health of your inventory helps ensure correct pricing strategies and optimize stock levels. Moreover, inventory accounting involves valuing and reporting on the physical inventory held by a business, which is fundamental to maintaining accurate financial records.
Key Components of Inventory Accounting
Inventory accounting consists of several key components that provide a comprehensive picture of a business’s inventory health. Accurate inventory costing offers a clear view of the largest asset, aiding in informed financial decisions within the inventory accounting process.
One of the main challenges in obtaining an accurate picture of inventory is knowing the precise levels and product-level sales data. Frequent cycle counting helps in tracking daily, monthly, and yearly sales and losses, contributing to inventory accuracy.
Beginning Inventory
Beginning inventory represents the total value of inventory at the start of an accounting period. This value is critical as it serves as the baseline for calculating inventory values and changes over the period. For instance, if a company starts the year with $10,000 in inventory, this figure must be recorded on the balance sheet.
Recording beginning inventory accurately ensures financial statements reflect true accurate inventory records, supporting effective management strategies.
Ending Inventory
Ending inventory is the total value of inventory at the end of an accounting period and is crucial for determining profitability. This value serves as the beginning inventory for the next period. If a company’s ending inventory is valued at $25,000, accurate recording is crucial for correct financial reporting.
Factors like cost flow assumptions and the timing of sales can significantly affect the cost of ending inventory.
Inventory Valuation Methods
Before:
The choice of inventory valuation method significantly impacts financial statements, particularly the cost of goods sold (COGS) and net income. The main inventory valuation methods include FIFO, LIFO, the weighted average method, and the specific identification method. Each method has its unique advantages and is suitable for different business scenarios.
After:
The main inventory valuation methods include:
- FIFO (First In, First Out)
- LIFO (Last In, First Out)
- Weighted Average Method
- Specific Identification Method
- Inventory Costing Methods
Each method has its unique advantages and is suitable for different business scenarios.
Selecting the most appropriate method requires knowledge of industry standards, inventory nature, and regulatory requirements.
FIFO Method
The FIFO (First-In, First-Out) method assigns costs based on the chronological order of purchases. This means that the oldest inventory is sold first. For example, if Mary applies FIFO to her wine glasses inventory, she assigns $12 for the first 50 glasses and $16 for the next.
FIFO often results in a lower cost of goods sold and higher reported profits, reflecting recent prices, but tracking costs for different batches can be challenging.
LIFO Method
LIFO (Last-In, First-Out) is an inventory method where the most recent purchases are sold first, making it suitable for businesses experiencing inflation. Under LIFO, the last stock added is sold first, resulting in higher costs of goods sold and lower taxable income during periods of rising prices.
LIFO is complex, burdensome to maintain, and only permitted under GAAP in the United States.
Weighted Average Method
The weighted average method averages costs over time, minimizing price fluctuation impacts. The unit cost is calculated by dividing the total cost by the weighted average cost of the total number of units.
For instance, Lisa calculates the average cost of her lipsticks by dividing the total inventory purchased, $1250, by the total units, 90. This method works well for businesses with stable prices, providing balanced inventory valuation.
Specific Identification Method
The specific identification method assigns a specific cost to each individual item in inventory. Ideal for unique or high-value items, this method allows precise cost tracking. If the total inventory cost is $800 and a painting sells for $200, the remaining inventory cost is $600.
This method requires confident identification of SKU location, cost, and sale amount.
Inventory Accounting Systems
Comparing the periodic and perpetual inventory system reveals their unique advantages and drawbacks. The periodic system records inventory changes at specific intervals, often leading to outdated information between updates. In contrast, the perpetual system provides real-time updates, recording sales and costs simultaneously.
While the perpetual system offers immediate insights for decision-making, it comes with higher operational costs. Frequent physical inventory counts are crucial for the periodic system to ensure accuracy.
Cost of Goods Sold (COGS)
Cost of Goods Sold (COGS) encompasses all direct expenses related to producing goods sold, differentiating it from indirect costs like marketing. Understanding COGS is essential for determining gross profit and production costs, encompassing raw materials, labor, and manufacturing costs.
Beginning inventory is essential for determining COGS, while ending inventory value is vital for calculating profitability. Accurate COGS calculation influences overall profitability and tax obligations.
Inventory Management Techniques
Effective inventory management is essential for optimizing costs and availability, directly impacting profitability and operational efficiency. Techniques like ABC Analysis categorize inventory into groups based on popularity and carrying costs, helping to optimize stock management.
Safety stock helps businesses handle unexpected demand spikes and supply chain delays. Reviewing vendor relationships regularly can lead to better contract terms and optimized inventory costs.
Impact of Inventory Accounting on Financial Statements
Inventory accounting methods significantly influence financial statements, particularly the valuation of total assets on the balance sheets. Different methods can impact tax liabilities by altering reported net income and COGS. For example, LOFO can alter both the income statement and the balance sheet, affecting financial reporting.
The choice of inventory accounting method directly impacts gross profit and net income calculations.
Handling Inventory Discrepancies
Inventory discrepancies arise from mismatches between recorded and actual physical inventory levels. This difference can lead to various issues in inventory management. Regular inventory reconciliation is essential to ensure accuracy. Documenting discrepancies helps businesses uncover underlying issues and improve inventory processes.
Inventory management software streamlines reconciliation and minimizes manual errors. Regular inventory checks enhance accuracy and help catch discrepancies early, contributing to effective inventory control.
Advanced Inventory Costing Techniques
Advanced inventory costing techniques are crucial for optimizing operations and profitability. These techniques involve assigning expected costs of material, labor, and overhead to inventory.
These advanced methods help businesses refine inventory management strategies and improve financial outcomes.
Highest Cost Inventory (HIFO)
The HIFO method involves selling the highest costing inventory first. This approach can reduce taxable income or asset value temporarily. However, GAAP or IFRS do not recognize it.
While HIFO can be beneficial in certain scenarios, its lack of recognition under major accounting standards limits its widespread application.
Lowest Cost Inventory (LOFO)
The LOFO (Lowest Cost First) method prioritizes the sale of the least expensive inventory items. This changes COGS by removing the lowest cost inventory first, potentially impacting profitability.
Retail Inventory Method
The retail inventory method is particularly beneficial for retailers needing quick inventory estimates. It works best when there is a standard markup within broad product lines. The cost-to-retail ratio is determined by taking the cost of a product. This amount is then divided by the retail price.
For example, the estimated ending inventory at cost is calculated as $8,000 using this method.
Inventory Write-Offs and Adjustments
Inventory write-offs involve removing unsellable inventory items from the recorded stock due to factors like theft, damage, or spoilage. This process typically includes a journal entry that debits the COGS account and credits the Inventory account.
Write-offs reduce the inventory balance on the balance sheet and recognize an impairment expense on the income statement.
Choosing the Right Inventory Accounting Method
Choosing the right inventory accounting method requires understanding current and future business needs. Considerations include management style, business objectives, and local tax laws. Consistency in methods is vital for fair financial reporting and accurate tax obligations.
Consulting financial professionals and using accounting software can enhance efficiency and accuracy in inventory tracking.
Integrating Accounting Software for Inventory Management
Integrating accounting software with inventory management systems offers benefits like real-time updates, reduced manual errors, and improved financial reporting. Automation helps prevent issues like overselling or stock shortages.
Linking these systems allows for automatic generation of purchase orders when stock levels reach predetermined levels, saving time and reducing workload.
How Argos Software Enhances Inventory Accounting
Argos Software offers integrated tools that streamline inventory accounting, improve financial accuracy, and support regulatory compliance. Designed for efficiency and visibility, Argos aligns with best practices to help businesses manage inventory and costs effectively.
Key Inventory Accounting Features:
- Real-Time Valuation & Costing Methods: Argos supports FIFO, LIFO, weighted average, and specific identification, enabling accurate real-time inventory valuation and cost of goods sold (COGS) tracking.
- Integrated Financial & Inventory Data: Inventory and accounting systems work together seamlessly, ensuring that beginning and ending inventory values are automatically reflected in financial reports.
- Cycle Counting & Discrepancy Management: Built-in cycle counting tools help maintain inventory accuracy and generate audit-ready reports for easy reconciliation and write-offs.
- Comprehensive Cost Tracking: Argos provides detailed, item-level cost tracking to support accurate financial reporting and profitability analysis.
- Scalable Multi-Site Support: Whether managing a single location or a multi-warehouse operation, Argos centralizes inventory data and supports consolidated reporting.
With Argos Software, businesses gain the tools needed to maintain inventory accuracy, reduce errors, and improve overall financial health.
Summary
Mastering inventory accounting involves understanding various methods and techniques to ensure accurate financial reporting and optimized inventory management. From basic concepts like beginning and ending inventory to advanced costing techniques, each aspect plays a critical role in a business’s financial health.
By implementing the insights shared in this guide, businesses can improve their inventory management strategies, reduce discrepancies, and enhance overall profitability. Remember, the right inventory accounting method can make all the difference in achieving financial success.
Take Control of Your Inventory Accounting
Ready to improve accuracy, reduce errors, and strengthen your financial reporting? Discover how Argos Software simplifies inventory accounting with real-time insights, integrated systems, and powerful tracking tools.
Frequently Asked Questions
What is the importance of inventory accounting in a business?
Inventory accounting is vital for ensuring accurate financial reporting and maintaining profitability, as it provides crucial insights into a business’s financial health and aids in meeting tax obligations.
How does the FIFO method impact financial statements?
The FIFO method leads to lower cost of goods sold and higher reported profits, resulting in a more favorable portrayal of financial health. This approach accurately reflects ending inventory values by aligning them with recent prices.
What is the difference between the periodic and perpetual inventory systems?
The key difference lies in the timing of inventory updates; the periodic inventory system records changes at set intervals, while the perpetual inventory system updates inventory data in real-time. Therefore, the perpetual method offers more accurate and current information on inventory levels.
Why are inventory write-offs necessary?
Inventory write-offs are essential to accurately reflect the actual value of your stock by removing unsellable items from financial statements. This practice helps maintain clear financial health and prevents overstatement of assets.
How can integrating accounting software improve inventory management?
Integrating accounting software enhances inventory management by providing real-time updates and reducing manual errors, leading to more accurate financial reporting and improved oversight. This automation streamlines operations and boosts overall efficiency.