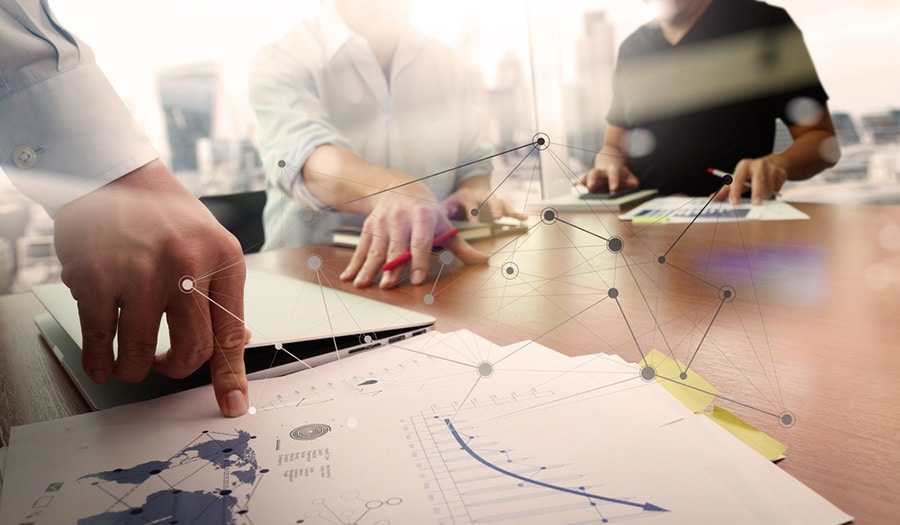
The global economy forces partnerships among companies throughout the world. While the obvious benefits of such far-flung agreements are reduced labor and manufacturing costs, as well as speed of delivery, there are potential risks. Breakdowns in the supply chain, however minor, are particularly threatening to the overall process because they can affect all parties, both upstream and downstream. And no one wants a slowdown.
With so much at risk, how can companies minimize or mitigate disruptions in their supply chain? What areas are worth looking at for risk management? What habits can a company adopt to prepare for legal disruptions that might be disastrous? Here are a few ways to start:
1. Get to know your supply chain neighbor
No matter where you are along the supply chain, do what you can to get a full assessment of the company you rely upon the most to get products moving. For example, manufacturers need to have comprehensive knowledge of their suppliers, distributors, and retailers while all three should get to know the manufacturer. This should involve establishing key contacts, creating protocol for notifying upstream and downstream partners of potential problems, and other due diligence efforts that will keep supply moving.
2. Make sure your contracts are comprehensive
The global nature of your partnerships can mean you are at the mercy of laws of other jurisdictions, which exposes you to a wide range of liability. Before you sign, make sure your contracts are comprehensive and protect you by giving you legal recourse against whichever responsible party in case of a supply chain disruption or product recall. Know your rights, but also know your obligations and the obligations of others so risk is shared.
3. Get insurance that is airtight
If you are involved in a liability claim or another kind of supply chain dispute you don’t want to be either uninsured or underinsured. You need to understand every kind of risk involved and have insurance that has you covered. For example, a class action lawsuit involving food product recalls can create liability exposure in the millions of dollars. You need to have insurance that forecasts scenarios like that to make sure you are protected.
4. Get the details right
Good record keeping may feel like a chore, but it will save you when disaster strikes. Besides making sure that all your contracts are executed correctly, make sure you properly archive paperwork related to every aspect of your business: contracts, insurance policies, and commercial documents related to equipment and facilities, etc. You don’t want to be stuck in the dark in case of a liability claim or an equipment breakdown.
5. Seek home court advantage
The challenges of foreign partnerships can include slow communication and the difficulty of obtaining access to information. But you may also be exposed to rules that may be outside the jurisdiction of the Canadian and U.S. court system. The way to reduce that risk is to secure home court advantage through arbitration clauses in your contracts or via your terms and conditions.
Want more tips? Check out this article in Inbound Logistics that gives you more ways to reduce risk when operating with global supply partners.
What do you do prepare for potential problems in your supply chain? Give us your tips in the comments below. Visit argosoftware.com or call us at (888) 253-5353 to set up a demo or learn more about our suite of products for Logistics Service Providers (3PLS and Transporters).