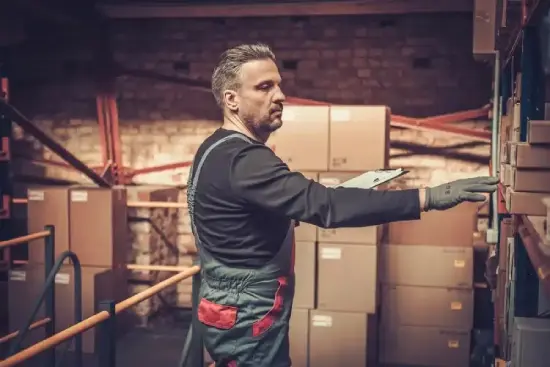
If you’re responsible for overseeing the operations of a warehouse or 3PL, then you know that order picking is a critical component of success. But what are the best practices for order picking in warehouse facilities and what strategies can you employ to improve efficiency and accuracy in your warehouse?
In this blog post, we will take a look at some tips and techniques for order picking improvements to consider for your warehouse. Read on to learn more about how warehouse managers and operators can improve their warehouse picking process.
What is Order Picking in a Warehouse?
Order picking is the process of retrieving items from a warehouse to fill customer orders. This can be done manually or with the help of order picking equipment such as RF scanners, robotic order pickers, forklifts, and conveyor systems. In most modern warehouse operations, software is used to streamline the picking process and track inventory levels.
Why is Order Picking So Important?
Order picking is a critical part of the order fulfillment process. Inaccurate or slow order picking can lead to delays in shipments, unhappy customers, and increased costs, therefore it is crucial to have an efficient picking system in place.
Here are some of the main benefits of implementing an efficient order picking process:
- Reduced Cost. An efficient order picking system can help to reduce the overall cost of order fulfillment. This includes both the direct costs associated with order picking (e.g., labor, equipment, etc.) and the indirect costs that come from errors and delays (e.g., shipping, customer service, etc.).
- Increased Efficiency. An efficient warehouse picking system can help to increase the overall efficiency of your warehouse operations. This, in turn, can lead to higher productivity and lower operating costs as you meet customer demand.
- Improved Customer Satisfaction. Customers expect their orders to be shipped quickly and without errors. Fast and accurate order picking is essential for providing good customer service. If you are unable to provide the best service, then you’ll likely lose business to your competitors.
- Improved Performance of Warehouse Workers. An efficient order picking system can help to improve the performance of your warehouse staff. Staff assigned to selecting inventory who are able to quickly and accurately pick orders will be more productive and have a lower rate of errors. Because the job becomes uncomplicated, it can also keep your team motivated and boost morale.
The Picking Process: Common 3PL and Warehouse Order Picking Methods
There are several different warehouse picking strategies that can be used in a supply chain distribution center. Determining the best strategy for your operation depends on a number of factors, including the type of products to be picked, warehouse size, and order volume.
Some popular order picking methods include:
Discrete or Single Order Picking
Discrete order picking, also known as single order picking, is an order fulfillment method in which each order is filled individually. Discrete order picking can be done with a traditional paper-based order picking system or with the help of warehouse management system (WMS) software. This method is typically used for orders that are small or require a high degree of accuracy.
Batch Picking
Batch picking is a distribution facility picking method where multiple orders are picked at the same time. This can be done by assigning a picker to each order or by combining multiple order processing together that need similar items. Batch picking can help to improve order-picking efficiency by reducing the number of trips made to each SKU location.
Zone Picking
With zone picking, inventoried items are grouped together by location in the warehouse. Each picker is assigned to a specific zone and responsible for filling orders from that zone. Zone order picking can help to improve picking efficiency by reducing travel time.
Pick and Pass
Pick and pass is another name for zone picking. In this warehouse picking method, all items within a zone are picked, then passed off to the order picker in the next zone.
Wave Picking
Wave picking is another common strategy for distribution facilities or 3PLs. In this scenario, order pickers are assigned to waves or groups of orders, and items are picked for all orders in the wave at the same time. Wave picking factors in warehouse employee scheduling to optimize order picking instead of assigning orders on a first-come, first-serve basis.
Voice Picking
Voice picking uses voice recognition technology to track and fill orders. In a voice-picking system, 3PL or warehouse employees are given a headset and microphone that they use to vocally pick orders. The headset is connected to the facility’s WMS, which gives the picker real-time order information. Voice picking can help to improve order accuracy and efficiency by reducing the need for paper picking lists.
As we said, the right warehouse order picking method will depend on a number of factors. Read on for information on equipment types to consider that can increase picking efficiency.
Warehouse Picking Equipment
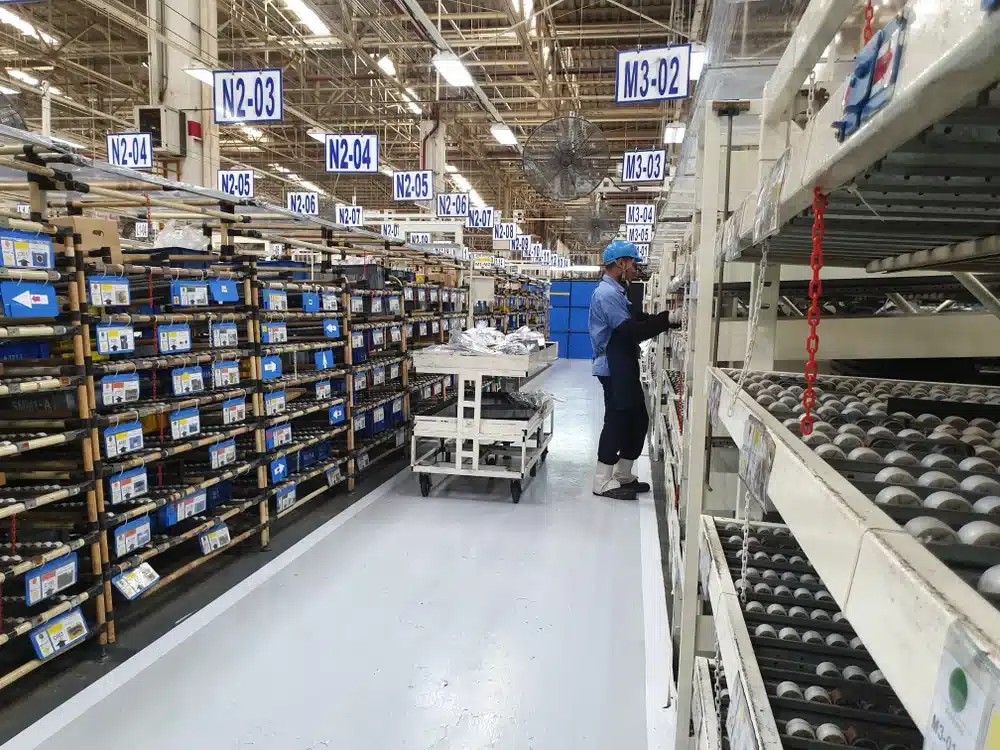
Having a well-run order fulfillment operation requires more than just having the right picking strategy in place. You’ll also need to have the right order picking equipment for your warehouse. Some common equipment includes RF scanners, order pickers, forklifts, conveyor systems, and automated storage and retrieval systems (AS/RS). Let’s discuss each of these here:
- Mobile RF Scanners: A mobile RF, or radio-frequency, scanner is a staple in most warehouses these days. These handheld devices are used to scan barcodes and track inventory. RF scanners can be used for a variety of tasks in the warehouse, including order picking, SKU putaway, and cycle counting.
- Order Pickers: Order pickers are another commonly used piece of picking equipment. Order pickers come in a variety of shapes and sizes, and are typically electric. They have a platform that the operator stands on, as well as a basket or shelf for holding items. These units are used to pick orders from high shelves or racks in the warehouse where it would be difficult or dangerous for a person to reach.
- Forklifts: Forklifts are another common type of picking equipment. Forklifts can be used to load and unload trucks, move pallets of goods throughout a distribution facility, and pick orders. Having a forklift in your warehouse can help to improve picking efficiency by reducing the need for additional labor to pick individually and/or by hand.
- Conveyor Systems: Conveyor systems are often used in order picking operations. Conveyor systems can help to move items around the warehouse and can be used to bring orders to the picker faster than they could retrieve them themselves. These systems can be used to move items from one location to another or can be used to create a continuous loop from which orders are picked.
- Automated Equipment: Automated storage and retrieval systems (AS/RS) are a type of picking equipment that is becoming more popular in warehouses. AS/RS systems can help to automate the picking process by storing items and bringing them to the order picker as needed. This can help to improve picking efficiency and accuracy.
Order Picking in Warehouse Best Practices
There are several best practices that can help to improve picking efficiency in your warehouse. These include:
Use Order Picking Software
Order picking software can help to optimize order pick routes and reduce travel time. Argos WMS Software is a popular picking and inventory management software solution for 3PLs, distribution centers, and agricultural businesses.
Train Order Pickers
Order pickers should be properly trained on the picking software and equipment being used in the warehouse. This will help to ensure that they are using the system correctly and efficiently.
Optimize Warehouse Layout
The layout of the warehouse can have a big impact on picking efficiency. Items should be stored in an easily accessible location and order pickers should have a clear path to necessary inventory. This will help to reduce travel time and improve order accuracy.
Using Order Picking Equipment
As discussed earlier, your warehouse or 3PL can benefit by having the right equipment supplemented by an efficient order picking operation. Picking equipment can help to improve picking efficiency by reducing travel time and manual labor.
Implementing these best practices can help to save time, improve order accuracy, and improve efficiency in your warehouse operations.
Order Picking and Warehouse Profitability
Order picking is a critical part of the warehouse operation and can have a big impact on profitability. An efficient order picking system can help to reduce order cycle times, increase accuracy, and improve customer satisfaction, thus saving money and improving your bottom line.
How WMS Software Helps with Picking Orders
WMS software can help to optimize order picking in your distribution facility by providing real-time visibility into inventory levels and order picker locations. WMS systems can also be used to schedule needed labor, create pick routes, and track order picking progress.
Argos Software: Designed for 3PL and Distribution Centers
Argos is a comprehensive warehouse management system software designed for 3PLs and distribution centers. Some features include:
- order entry
- order tracking
- order consolidation
- picking optimization
- shipping integration
- inventory management
Argos can help to improve order fulfillment and picking efficiency in your warehouse. For more information on Argos Software, contact us today.
How to Choose the Right Order Picking Strategy For Your Own Warehouse?
There are a few things you should consider when choosing a picking strategy for your warehouse:
- The type of products you’ll be picking (e.g. heavy, light, fragile)
- The order volume (e.g. number of orders per day)
- The size and layout of your warehouse
- Your budget for picking equipment
You’ll also need to decide which picking strategy is best for your warehouse. As we’ve said, there are a few common picking strategies, including discrete picking, batch picking, zone picking, and wave picking among others.
Once you’ve chosen your picking system, you’ll need to implement it with the help of inventory and order control WMS software like Argos. If you need help choosing the right order picking strategy or implementing a picking system, contact us today. We’ll be happy to help you choose the best order picking strategy for your warehouse.
Conclusion
Order picking is a critical part of the warehouse operation and can have a big impact on profitability. An efficient order picking system can help to reduce order cycle times, increase accuracy, and improve customer satisfaction.
Choosing the right picking methods can also make a big difference in your order picking process. Common warehouse picking strategies include discrete picking, batch picking, zone picking, pick and pass, and more. For more information on how Argos Software can help your warehouse operation, please contact us.